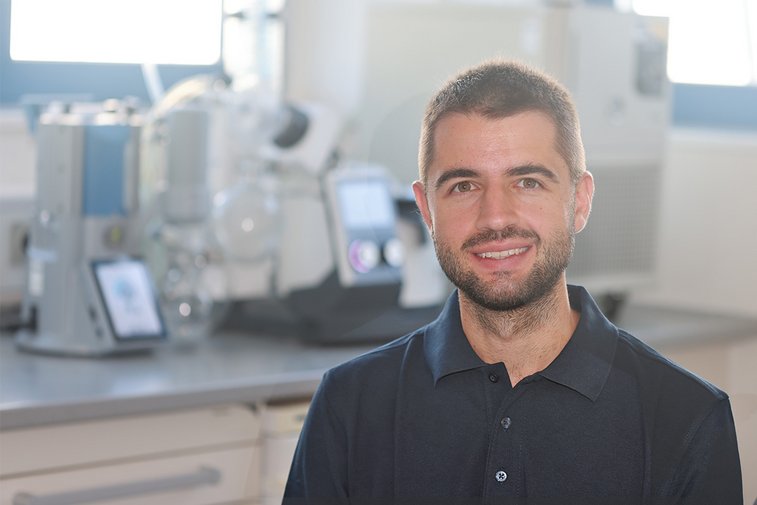
Dr. Florian Heinrich shares his practical knowledge of rotary evaporation and optimum vacuum control.
© VACUUBRAND
As a PhD chemist with many years of laboratory experience, Dr. Florian Heinrich has spent numerous hours working with rotary evaporators. One thing has become clear: the right vacuum is crucial for a successful process. In this article, he shares his practical insights for efficient and safe work with the rotary evaporator.
1. Regular leak testing: fixing imperfections
A frequently neglected but crucial measure: regularly check the tightness of your system. To do this, evacuate the empty and dry rotary evaporator, close the vacuum supply, and monitor the pressure rise. A rapid increase indicates leakage that needs to be fixed.
2. Delta-20 rule: achieving efficient evaporation
The temperature of the heating bath should be about 20°C higher than the desired evaporation temperature in the evaporating flask. At the same time, the cooling temperature should be at least 20°C lower than the evaporation temperature. For example, for an evaporation temperature of 40°C, a heating bath setting at 60°C and cooling at a maximum of 20°C is recommended.
3. Optimal flask fill level: ensuring maximum yield
The evaporating flask should be filled not more than 50% of its capacity. A fill level that is too high increases the risk of bumping and conclusive contamination.
4. Adjusted rotation speed: managing viscosity
For better efficiency, the rotation speed can be adapted to the properties of the material being evaporated. For low-viscosity liquids, a higher speed promotes evaporation by increasing the surface area. For highly viscous solutions, lower speeds are recommended to avoid liquid accumulation on the flask walls and to ensure effective heat transfer.
5. Application of vacuum before immersing the flask: reducing vapor
A common mistake: The flask is lowered into the heating bath before applying vacuum. This causes volatile solvents to distribute throughout the entire system before the vacuum pump is active. The consequence: The pump has to work against these vapors, leading to longer process times and potentially straining the vacuum pump.
6. Optimal process pressure: avoiding bumping and foaming
The ideal process pressure corresponds to the vapor pressure of the solvent, where evaporation and condensation are in equilibrium. Important to understand: Lower pressure is not necessarily better! A vacuum that is too low can lead to bumping and foaming, which can contaminate the sample.
7. Ratio of evaporation and condensation: achieving perfect balance
A simple visual indicator: Observe the condensation on the cooling coil. When about two-thirds of the coil is covered with condensate and the upper third remains dry, a good balance is established.
8. Correct hysteresis in two-point control: promoting valve longevity
When working with a manual two-point control system, the hysteresis (pressure fluctuations between minimum and maximum) should be about 10% of the set pressure. A hysteresis that is set too narrow leads to frequent switching of the valve, which can cause wear and be acoustically disturbing.
9. Automatic vacuum control: saving time and energy
Modern speed-controlled VARIO® vacuum pumps from VACUUBRAND can manage the process fully automatically. They independently detect the boiling point and continuously adjust the pressure to changing conditions. This not only saves time but also results in gentler distillation processes and lower energy consumption. For more demanding solvents, which tend to bump due to their high surface tension, the automatic mode offers additional sensitivity adjustment options for optimal distillation results.
10. Regular fill level monitoring: preventing contamination
Monitor the fill levels in all receiving flasks throughout the entire process. An overfilled receiving flask can lead to backflow and contaminate the sample. When using a pumping unit by VACUUBRAND, regularly check the separator at the pump inlet (AK) as well as the exhaust vapor condenser (EK).
Conclusion
The rotary evaporator and the associated vacuum control are not rocket science, but they do require attention to detail. With these practical tips, you will not only improve the efficiency of your distillation processes but also take care of your equipment and, most importantly, your valuable samples.
Remember: Demand-oriented vacuum control is crucial. When selecting a new vacuum pump, utilize available selection aids such as the "Vacuum Pump Selection Guide" to find the optimal solution for your application.